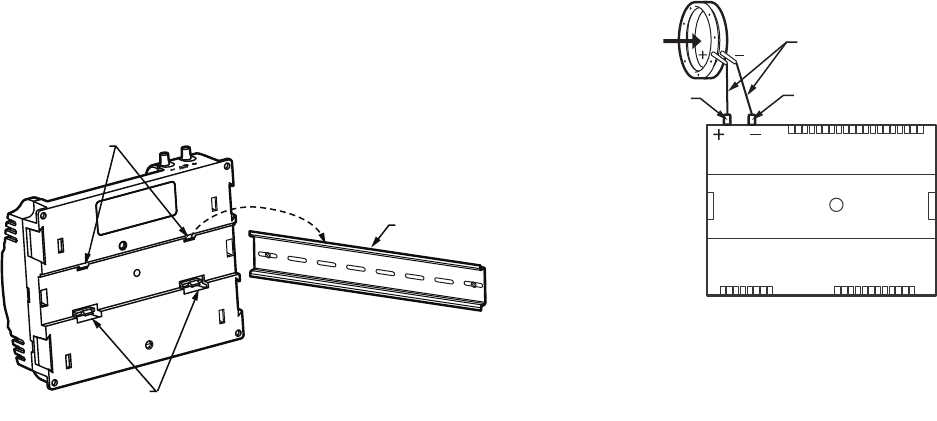
SPYDER® BACNET® PROGRAMMABLE CONTROLLERS
63-2689—05 6
Panel Mounting
The controller enclosure is constructed of a plastic base plate
and a plastic factory-snap-on cover.
NOTE: The controller is designed so that the cover does
not need to be removed from the base plate for
either mounting or wiring.
The controller mounts using four screws inserted through the
corners of the base plate. Fasten securely with four No. 6 or
No. 8 machine or sheet metal screws.
The controller can be mounted in any orientation. Ventilation
openings are designed into the cover to allow proper heat
dissipation, regardless of the mounting orientation.
DIN Rail Mounting (PUB1012S, PUB4024S,
PUB6438S, PVB4024NS and PVB6438NS)
To mount the PUB1012S, PUB4024S, PUB6438S,
PVB4024NS and PVB6438NS controllers on a DIN rail
[standard EN50022; 1-3/8 in. x 9/32 in. (7.5 mm x 35 mm)],
refer to Fig. 8 and perform the following steps:
1. Holding the controller with its top tilted in towards the DIN
rail, hook the two top tabs on the back of the controller
onto the top of the DIN rail.
2. Push down and in to snap the two bottom flex connectors
of the controller onto the DIN rail.
IMPORTANT
To remove the controller from the DIN rail, perform the
following:
1. Push straight up from the bottom to release the top
tabs.
2. Rotate the top of the controller out towards you and
pull the controller down and away from the DIN rail to
release the bottom flex connectors.
Fig. 8. Controller DIN rail mounting (models PUB1012S,
PUB4024S, PUB6438S, PVB4024NS and PVB6438NS).
Piping (PVB0000AS, PVB4022AS,
PVB4024NS, PVB6436AS and
PVB6438NS)
Air flow Pickup
For PVB0000AS, PVB4022AS, PVB4024NS, PVB6436AS and
PVB6438NS, connect the air flow pickup to the two restrictor
ports on the controller (see Fig. 9).
NOTES:
— Use 1/4 inch (6 mm) outside diameter, with a 0.040
in. (1 mm) wall thickness, plenum-rated 1219 FR
(94V-2) tubing.
— Always use a fresh cut on the end of the tubing
that connects to the air flow pickups and the
restrictor ports on the controller.
Connect the high pressure or upstream tube to the plastic
restrictor port labeled (
+), and the low pressure or downstream
tube to the restrictor port labeled (
-). See labeling in Fig. 9.
When twin tubing is used from the pickup, split the pickup
tubing a short length to accommodate the connections.
NOTES:
— If controllers are mounted in unusually dusty or dirty
environments, an inline, 5-micron disposable air
filter (
use 5-micron filters compatible with
pneumatic controls)
is recommended for the high
pressure line (marked as
+
) connected to the air
flow pickup.
— The tubing from the air flow pickup to the controller
should not exceed three feet (0.914 m). Any length
greater than this will degrade the flow sensing
accuracy.
— Use caution when removing tubing from a connec-
tor. Always pull straight away from the connector or
use diagonal cutters to cut the edge of the tubing
attached to the connector. Never remove by pulling
at an angle.
Fig. 9. Air flow pickup connections (PVB0000AS,
PVB4022AS, PVB4024NS, PVB6436AS and PVB6438NS).
Power
Before wiring the controller, determine the input and output
device requirements for each controller used in the system.
Select input and output devices compatible with the controller
and the application. Consider the operating range, wiring
requirements, and the environment conditions when selecting
input/output devices. When selecting actuators for modulating
applications consider using floating control. In direct digital
control applications, floating actuators will generally provide
control action equal to or better than an analog input actuator
for lower cost.
Determine the location of controllers, sensors, actuators and
other input/output devices and create wiring diagrams. Refer to
Fig. 17–Fig. 23 beginning on page 14 for illustrations of typical
controller wiring for various configurations.
DIN RAIL
TOP TABS
BOTTOM FLEX
CONNECTORS
M16815
M23556A
AIR FLOW
PICKUP
ΔP
1
2
3 4 5 6
7 8
1 0 9 2 3 4 5 6 7 8 0 9
1 1 1 1 1 1 1 1 1 2 1
1
2
3 4
5
6
7 8
0
9
2
2 2
2 2
2
2
2 2
3
3
1
2
3 4
5
6
7 8
0
9
3
3
3
3 3
3 3
3 4
RESTRICTOR
PORT
RESTRICTOR
PORT
CONNECTOR
TUBING